Quick Die Change Systems for Forging and Trim Presses
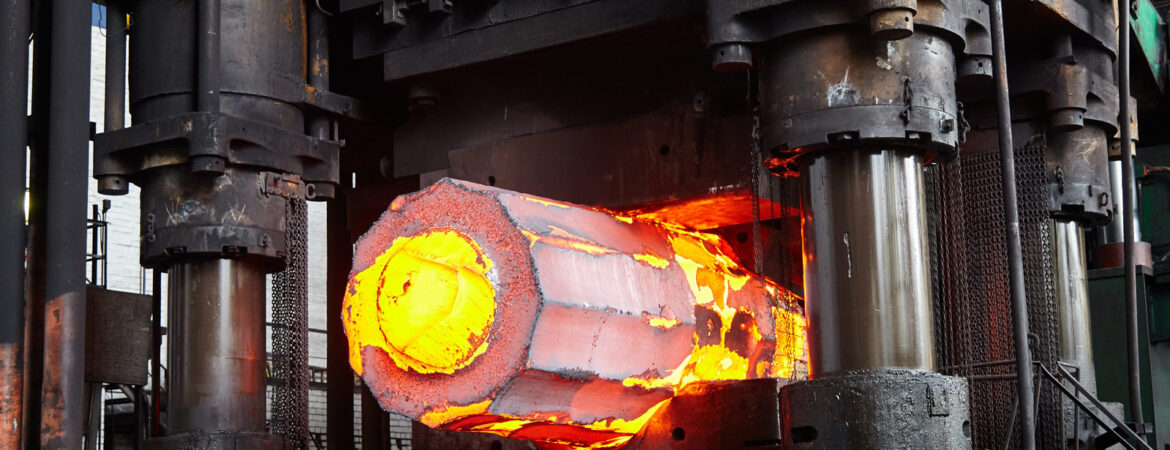
Forging Die Clamping and Positioning
Replace labor-intensive bolt tightening
![]() |
Wedge Clamps for ForgingWedge Clamps are designed to suit the adverse conditions of forging while minimizing press downtime. The retracting clamping bolt and its rugged housing help to isolate forging heat and shock loads from the hydraulic circuit. The wedge clamp’s self-locking tapered bolt clamps on a mating 20° beveled surface on the die. Wedge clamps with a vertical clamping bar can be integrated into the lower master die set. The bar further isolates the hydraulics from the heat of the process and can be removed during the tool change.
Advantages:
|
![]() |
Following manual positioning of the clamping nut against the clamping edge, the internal gear will be operated by turning the hexagon socket. As a result of the gear transmission, the tightening torque is multiplied. To reliably ensure the required clamping force, we recommend using a torque wrench.
|
Don’t miss us at Forge Fair on May 23-25, 2023 in Cleveland >
Please send me more information
![]() |
Move Dies During ProductionBlock Cylinder | B1.5091Use block cylinders with position monitoring to move dies during production. Block cylinders, single or double-acting, are made of high alloy steel, bronze alloy, and special aluminum alloys. They can be installed in any position and have a max stroke speed of 0.25 m/s. ROEMHELD block cylinders do not leak oil when static. Stroke leakage is at a minimum due to the double piston sealing.
|
![]() |
Clamping for Forging Trim PressesMore Clamping OptionsTrim presses do not see the severe environment and tremendous forces seen in the forge press. Because of this, there are more clamping choices, such as hollow piston, sliding, fixed mounted clamping bar, and others. When the trim press is configured with hydraulic clamps and die lifters to provide a quick die change, there are many advantages including the elimination of manual clamping on hot dies, single minute change of dies; which means more press uptime, and die lifters and die supports to provide a rolling surface for ergonomic die exchange.
|
Moving and Handling Forging Dies
Move large dies with ease
![]() |
Quick and Safe Die Changes Up to 50 Tons
|
![]() |
Safe and Gentle Transport of Heavy DiesDie CartsPowered or manual carts that transport dies up to 3600 lbs., and helps the dies to be safely transported efficiently.
|
![]() |
Roll Your Dies Easily Into PlaceDie LiftersRoller bars and ball bars with hydraulic or spring lifting of the individual rollers for easy die movement.
|
![]() |
Control All the Clamps and Lifters in the Die Change SystemHydraulic Power UnitsFor operating hydraulic clamping fixtures and other handling and clamping systems on presses.
|
Please send me more information
Hydraulic Vs. Mechanical Die Clamping
Hydraulic Die Clamping System Method
In today’s age of short runs and just-in-time deliveries, a hydraulic quick die change system for forging applications offers many advantages. The forging dies are locked in place with constant hydraulic pressure. The forces are commonly transmitted with clamps having tapered wedges mating with similar tapers on the die. Wedge clamps provide the advantage of repeatable hydraulic forces with the security of a locking mechanical wedge. Forging dies are quickly clamped and unclamped, thus saving time, which is important when the tools are changed frequently. Special materials and sealing technologies allow for the intense heat and conditions seen in forging.
Advantages:
- Ergonomic
- Short die changes times
- Little or no parts handling
- Less die movement = longer die life
- Compact clamp designs
- Large range of clamp sizes
- High, repeatable, and adjustable clamping forces
- Suitable for dual pressure clamp sequence
- Repeatable clamp forces
- Automation of the process is possible
Disadvantages:
- Higher investment cost
- Die modifications may be required
- Safety and monitoring system required.
- Hydraulic hose and tubing were added to the upper and lower die clamps
Mechanical Clamping Method
The clamping force on the forging die is often created by mechanical components such as t-bolts, strap clamps, and tapered wedges. The parts are installed and torqued down manually, so the clamping force is dependent on the skill of the die setter and the torque applied to the fasteners. As the size of the fasteners increases so does the required torque for safe clamp forces. After a brief operation of the press, the bolts may need to be retorqued. With these variables in mind, the repeatability of the clamping force may vary with the skill and physical abilities of the operator.
Advantages:
- Clamp components are relatively low cost
- Easy Handling
- Low maintenance cost
Disadvantages:
- Clamping and unclamping is all manual
- High torque and manual effort required
- Not ergonomic, prone to injury
- Time-consuming alignment and adjustment
- Loose clamp components during change
- Automation is not possible
What is Forging?
Forging is the process of shaping metal into its finished shape by pressing or hitting it against an anvil or die
ROEMHELD has the experience and can take the heat. We have the solutions for handling high temperatures with the correct products and systems suited to the needs of the forging process. By incorporating a Quick Die Change System into your facility, you can cut the time of your changeover by half, sometimes more. Die changing is easier for the operator, and may not require a highly skilled die setter. The die change time may also be shortened by preheating the tool outside of the press. In addition, you can expect the following:
-
More parts from one die, reducing die changes
-
Run-in periods can be reduced or eliminated since the die is securely clamped, centered, and located
-
Longer tool life, due to less wear and tear
-
Finished forging products have a constant high-quality level, even after the production of many pieces and frequent die changes.
-
Run-in periods are no longer necessary or can be considerably reduced, since the die is properly centered and located, additional alignment is not needed.
-
Highly repeatable clamping forces.
-
Reduce setup times
-
Reduce the risk of accidents with a safe die
change
-
Easy handling of heavy dies/tool